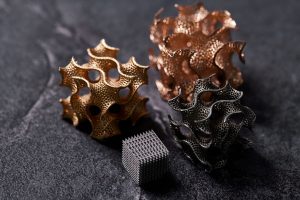
Events
Events At Cookson Industrial, we’re always at the forefront of innovation in the precious metals industry, and there’s no better way to showcase our cutting-edge
CONTACT US
- +44 (0) 121 233 8191
- sales@cookson-industrial.com
Events
Where You’ve Seen Us
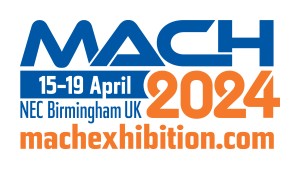
- MACH 2024, NEC Birmingham
Earlier this year, we were thrilled to be a part of MACH 2024 at the NEC in Birmingham, where we showcased our pioneering work in precious metal additive manufacturing. Visitors had the chance to see firsthand how our technology is redefining the use of precious metals across various industries.
- Advanced Engineering Trade Show, NEC Birmingham
October 2024 we exhibited at the Advanced Engineering Trade Show at the NEC, where we unveiled our latest innovations and demonstrated how our solutions can drive the future of engineering. This was the perfect venue to see how we’re pushing the boundaries of what’s possible with precious metals in modern industry.
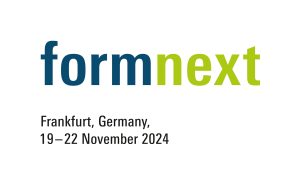
- Formnext, Frankfurt, Germany
We had the incredible opportunity to exhibit at Formnext in Frankfurt, the leading global exhibition for additive manufacturing. Here, we showcased our state-of-the-art 3D printing capabilities, including our pioneering work in 3D printed gold, silver and platinum.
- SpaceTech Expo, Bremen, Germany
The SpaceTech Expo in Bremen, one of the most significant events in the space technology sector. We presented our specialised solutions for the aerospace industry, focusing on how our precision metal components can contribute to the next generation of space exploration.
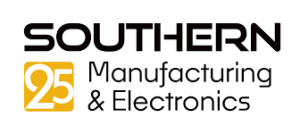
- Southern Manufacturing and Electronics show
We’re excited to announce that Cookson Industrial exhibited at Southern Manufacturing & Electronics 2025, the UK’s leading show for design, engineering, production, and procurement professionals.
Dates: 4th–6th February 2025
This must-attend event brought together the latest in production hardware, components, consumables, and cutting-edge technologies across diverse industries, including Aerospace, Automotive, Medical, Electronics, and more. It was a fantastic opportunity to discover innovative solutions and connect with professionals shaping the future of manufacturing.
At our stand, we showcased our precision-engineered solutions, including advanced additive manufacturing and high-performance components tailored to meet the demands of modern industry.
- IDS: Dental Industry and Dental Trade Fair
We had the opportunity to exhibit at IDS, the leading global trade fair for the dental community, we are excited to be here and showcasing our trusted dental alloys and products within the dental industry. Everything from Amalgam, Aristaloy and casting alloys both precious and non-precious. See us for your dental needs.
Where We’re Going Next
Stay Connected
We’re constantly exploring new opportunities and attending events that push the industry forward. Keep an eye on this page for updates on our exhibition schedule and discover where you can connect with us next. Whether you’re in the UK, Germany, or anywhere in between, we’d love to meet you and discuss how our expertise in precious metals can benefit your business.
We look forward to seeing you at one of our upcoming event
News & PR
Cookson Industrial and Renishaw Collaborate on Groundbreaking 3D Printing Innovation
We’re excited to announce a significant collaboration between Cookson Industrial and Renishaw, a global leader in precision engineering technologies, to advance the cost-effective 3D printing of platinum group metals (PGMs). This joint effort combines Renishaw’s expertise in metal additive manufacturing with Cookson Industrial’s deep knowledge of high-performance precious metals, creating groundbreaking advancements in this specialized field.
Together, we’re developing efficient, innovative solutions for producing components using some of the world’s most expensive materials, including platinum. These materials are traditionally difficult to shape and costly to work with, but our collaboration enables us to produce precision components with reduced waste and optimized cost-effectiveness.
This partnership also reflects our commitment at Cookson Industrial to pioneering advancements in precious metal applications for industrial sectors such as automotive, aerospace, and jewelry manufacturing. By harnessing Renishaw’s advanced additive manufacturing systems, we’re able to expand the range and complexity of components we can offer, achieving new benchmarks for efficiency, sustainability, and precision.
For more details on this exciting collaboration, visit the official announcement by Renishaw here. Stay tuned as we continue to drive innovation in the 3D printing of platinum group metals, delivering unprecedented value to our clients and partners.
________________________________________________________________________________________________
PRECIOUS OPPORTUNITIES – How New Additive Techniques are Unlocking the Next Era of Aerospace Research
On paper, fine jewellery and space engineering don’t seem to share much in common. One is considered more of an artform and the other a science.
It’s only when you look at precious metals that the connection becomes clearer. And now, with the latest developments in additive manufacturing (AM), you can essentially draw a direct line between the two.
This is a new area of research and development. Businesses with a history handling precious metals are now being asked to design, develop and deliver printed parts for use in some of the most extreme and technically challenging environments found anywhere on earth – and beyond. Without the right knowledge and production capabilities, however, this process is incredibly challenging.
So, what does best practice look like?
The connection between jewellery and space is less surprising when looking at the special properties of many precious metals. Take platinum. It has a very high melting point, is chemically inert and also highly resistant to corrosion and oxidation.
Yet, for all their use, precious metals have a high barrier of entry. They are – on the whole – incredibly expensive and even minor material losses from poor handling can lead to huge costs. To put it in context, five kilos of platinum loaded into the machine – roughly the amount required to print 6-8g parts – will cost in the region of £140,000. Even if a project were to lose
a fraction of this total material during the R&D or manufacturing process, the balance could easily run into the thousands.
Minimising material losses
The latest advances in AM have been nothing short of game-changing for the use of precious metals in space. In raw form, these materials are very difficult to manufacture using traditional methods as a fully dense structure is difficult to achieve. By its nature, subtractive manufacturing also creates a higher volume of waste and off-cuts, making it unsuitable for projects where the starting cost for production is already very high.
But there are also practical challenges. With platinum, welding, casting or brazing intricate shapes is very challenging. And it’s also difficult to hollow out – a key method for minimising weight in aerospace projects. This is not a problem with AM as the starting material is fundamentally different and parts are produced using only the exact amount needed.
Platinum is an advantageous material for AM, with densities of 99.9% easily achievable. But the right experience and in-house knowledge is needed to manufacture the right part at the right cost. Cookson, for instance, has extensive capabilities in alloy development given its background. Depending on a customer’s requirements, the company can choose from a standard selection of in-stock alloys or develop an entirely new one suited to the application in question. These alloys can use precious metals, such as rhodium or iridium, or non-precious metals in their makeup. They are then atomised into a powder suitable for AM and printed according to specified geometries. Working this way makes it far easier to produce complex designs that would otherwise be unattainable when using traditional methods. That is, unless a team is willing to invest a huge amount of time and money.
Still, AM on its own is not enough. Powdered precious metals are much harder to process effectively without the right tools. The risk of loss is still high – except at this point the amount of precious metal that could send a project into the red is effectively microscopic. Without the right control measures in place, a project could easily lose 10% or more of its powdered precious metal. An unworkable scenario.
This is a problem some organisations have faced when developing their own precious metal AM parts. And it’s the main reason why businesses like Cookson are now being brought into the fold. Cookson’s industrial division has invested heavily into its AM production and control measures in recent years, and this along with a long history in precious metals has drawn the attentions of major players in the aerospace sector.
One of the business’s standout projects has focused on the development of in-space water propulsion, using a platinum insert as the catalyst for a hydrogen-oxygen thruster. These so-called ‘green thrusters’ have received a lot of attention and investment in recent years. To date, there are none operational in space but there are hundreds of organisations working to launch the first. Green thrusters are deemed preferable to existing designs because they avoid the use of highly toxic liquid propellants.
Self-supporting structures allow highly complex parts to be manufactured quickly and accurately, whereas it is nearly impossible to manufacture the same parts traditionally – i.e with CNC machining, welding and casting. Platinum is a particularly strong candidate material for small satellite thruster applications due to a melting point around 1,768°C (3,214°F), making it highly resistant to extreme temperatures. Its oxidation resistance and chemical inertness also ensure longevity as there is a much smaller chance of degradation or adverse reactions with other materials.
Without the right processes in place – and knowledge of how to develop AM parts for critical environments – this figure is very difficult to achieve.
Selassie Dorvlo is Technical & Production Director at Cookson Industrial. For more information on precious metal AM, visit: www.cookson-industrial.com.
COOKSONGOLD UNVEILS NEW INDUSTRIAL DIVISION TO PIONEER PRECIOUS METALS USE IN ADDITIVE MANUFACTURING APPLICATIONS
Cooksongold has launched a new industrial division to pioneer the use of precious metal additive manufacturing (AM) for a range of performance-critical applications.
Part of HM Precious Metals, Cookson Industrial, will provide an end-to-end service comprising of consultancy, R&D, NPD and production. This includes conventional and subtractive manufacturing alongside its additive capabilities; all of which will be managed from its Birmingham head office and manufacturing site.
The use of precious metals in additive manufacturing offers organisations a new frontier for performance in extreme environments, where traditional alloys have failed to meet the thermal and material application challenges presented. Cookson Industrial aims to help organisations looking to explore the technology to de-risk their development, simplify their supply chains and shorten time to market.
The company develops and manufactures a broad range of gas atomised precious metal powders on site, including gold, silver, platinum and palladium powders; all of which are refined from recycled sources where possible.
All precious metal powders are available for purchase in small batches up to 15kg, or for use in Cookson Industrial’s state-of-the-art additive manufacturing facility in Birmingham. This currently comprises six EOS Precious M 080 and M 100 AM machines, alongside a Renishaw AM 500S Flex single laser AM machine.
Cookson Industrial has already partnered with the University of Birmingham to explore the development of precious metal alloys for additive manufacturing applications across the aerospace, healthcare and glass fibre manufacturing industries. Both organisations were jointly awarded a £750k Early-stage Prosperity Partnership funding from the Engineering & Physical Sciences Research Council (EPSRC).
Leveraging Cooksongold’s 100-year heritage in jewellery and luxury product manufacturing, the company is also currently working with Bentley Motors to manufacture a series of components for its Batur by Mulliner line.
Nikesh Patel, Head of Cookson Industrial, comments: “While the use of precious metals in additive manufacturing has largely been confined to the jewellery, luxury lifestyle industries, many more organisations are beginning to explore its potential for use in critical applications.”
Aerospace is seen as a key growth market for Cookson Industrial. The company is actively exploring new developments in satellite thruster design to help de-weight parts and reduce the volume of hazardous materials used in the manufacturing process compared to chemical thruster design.
Nikesh continues: “For extreme environments such as aerospace, where there is no room for compromise, the performance characteristics of precious metals can offer a whole new world of design parameters compared to traditional alloys.
“There is also a lot of dynamism in the UK aerospace sector with many legacy processes set for disruption. However, given the significant cost of the powders themselves – a full hopper often outweighs the purchase price of the AM machine – many organisations have struggled to fully commit to R&D. As we produce and print with our own powder supply, we can help derisk the process by offering the optimum parameters for powder production, storage and use. This will help reduce powder loss and the associated impact on project costs, while giving organisations access to one of the most innovative production environments in the UK.”
For more information, please visit: www.cookson-industrial.com
Minimising Material Losses- What Does Effective Handling Look Like for Precious Metal AM?
You don’t need to be an expert manufacturer to recognise the challenges posed by the use of precious metals in additive manufacturing.
Here, you’re dealing with a raw material that can cost hundreds of thousands per kilogram in solid form then atomising it into a fine powder that’s much harder to control. Without careful handling processes a project’s cost can easily spiral because the amount of material that could send a project into the red is – at this point – effectively microscopic.
Most will know roughly what’s needed to minimise material losses – care, attention to detail etc. But fewer people will know about the exact capabilities and interventions the best manufacturers use.
As such, this article can be thought of as a checklist for end users when identifying the right partner for their next AM project.
Does It Really Matter for the End User?
Identifying a partner that is able to effectively minimise material losses is becoming increasingly important as industries seek to incorporate more AM into their product development.
On one end you have aerospace research interested in the performance advantages certain precious metals can provide; on the other, you have luxury brands looking to create complex designs from gold, platinum and silver that would otherwise be impossible using traditional subtractive techniques. Sometimes luxury brands will also use AM purely for marketing purposes, as it implies a higher degree of sophistication or precision to potential customers.
These are all valid reasons for using AM. And they all emphasise the need for an organisation that’s familiar with the challenges of handling valuable material at this scale.
While businesses will typically pay upfront based on a quote from a company responsible for delivering AM parts, there is value in knowing precious metal powders will be handled with care. Working this way, there’s a much lower chance of loss and delay due to errors that are ultimately avoidable with the right steps in place. For instance, it’s not unreasonable to imagine a project
experiencing a weeks-long delay due to a dropped or misplaced quantity of precious material, especially those that are more difficult to source or on longer lead times. However, this threat can be managed if, like Cookson Industrial, an organisation keeps a bank of material on site or has access to a sister company’s inventory.
There is also a financial angle to consider. Good handlers will typically be more competitive, as they can accurately forecast for loss and recover a higher volume of raw material with the right in-house processes long before any work begins. In theory, these savings can then be passed on to the customer.
This is an area of AM Cookson Industrial has pioneered in recent years, benefitting from decades of experience working with precious metals, as well as a meticulous approach to material handling and recovery. The following steps provide an overview of the company’s process, which has been able to maintain an annual loss rate of less than 1%.
1. Designing for efficiency
The design phase plays a crucial role in reducing material waste. Good engineers will consider the topology of a part to minimise material usage while still maintaining part strength and functionality.
Developing parts with easily removable support structures is another option commonly used to reduce waste, as is consideration of orientation. Some products, for instance, will feature cavities that act as hiding spots for loose powdered metal. It’s worth removing or modifying these areas before production, if possible, particularly when the integrity of the design and its function can still be maintained.
2. Scrutiny at an atomised level
Atomisation is the first physical interaction a company will have with a precious metal in its powdered form, so it’s critical to get this stage right. Machine settings are important, as are the environment in which a precious metal is being handled.
Gas pressure and flow rates, for example, should be fine-tuned to maximise the yield of a desired particle size. Careful consideration of these areas will lower the chances of overspray and splatter, which can quickly build up if left to chance. Effective handing of precious metals will also minimise oxidation by only working in an inert gas environment. This is particularly important for more reactive metals, such as silver and red gold.
3. Keeping it clean
While perhaps not as critical, precious metal handling borrows a lot from medical environments, especially in terms of cross contamination. When dealing with a material like Rhodium – which averages around £135,000 a kilo – it pays to keep clean any brushes, surfaces and equipment used for processing.
The same principle applies to the build chamber. Effective manufacturers will have vacuum extraction and sieving stages to recapture loose metal powder particles, as well as steps to recover any powder stuck to the recoater blades.
Lint-free cloths used for wipe-downs can also be burned to recover powder, as the melting point of most alloys is very high. The same applies for lab wear, gloves, vacuum filters and hoses. All have significantly lower melting points than precious metals, allowing trace amounts of metal to be recovered.
4. Modified machinery
At the interface for any AM part build, the machines a manufacturer uses will have a major bearing on its ability to recover the maximum amount of material possible.
Cookson Industrial, for instance, has worked closely with machine tool OEM Renishaw to optimise the printing process, commissioning a customised version of its RenAM 500S Flex. Initial tests showed the machine was already capable of achieving a low powder loss level of 1.5%. However, for Cookson, a benchmark of 0.5% was set to maintain annual targets.
This customisation process was a success, reducing the volume of trapped powder by a further 95%. For the project in question, this allowed Cookson Industrial to retrieve the equivalent of a teaspoon of powder per cycle – equivalent to roughly £1,000.
5. Post-Processing
Post-processing steps such as support removal, polishing and finishing often lead to material loss. Collecting and refining this removed material can significantly reduce waste, especially for larger parts.
Mechanical methods such as milling and grinding should also be conducted in enclosed systems that allow for efficient collection and reuse of the metal shavings. Cookson Industrial has been able to perfect this process through several standout projects. For Bentley, the luxury car
manufacturer, we were able to print and mill a part to exact tolerances. This part was then hand polished and laser-marked by the assay office. The early stages saw all material collected and refined.
When printing it’s also advisable to weigh parts at every stage to gauge the anticipated level of loss, comparing the volume of material used against the volume of material still held in stock. Working this way, AM teams can then pinpoint potential problems wherever powder has been applied, allowing these areas to be corrected next time.
Given the nature of precious metal AM, it’s almost impossible to eliminate loss. However, with the right steps in place, a manufacturer can reach a point where only a fraction of a percentage of the total material is unaccounted for.
These steps are not foolproof – as they are only as effective as the level of care colleagues apply – though they do mark out the best companies working in precious metal AM. Why? Because good processes ultimately lead to better parts.
-Nikesh Patel. Head of Cookson Industrial.
For more information visit: www.cookson-industrial.com
Giving Green Thrusters a boost-Aerospace Testing International
There’s a new space race – albeit much quieter than the one which ran throughout the 1960s. This time it’s not about reaching new frontiers but instead focused on an issue very much of the 21st century: sustainability.
Green thrusters have been a major focus in aerospace since the 1990s, when the potential harms caused by traditional chemical propulsion became clear. Hydrazine, the inorganic compound often used in these systems, is a powerful monopropellant with a high energy density. These qualities have cemented its position as the dominant fuel used in spacecraft over the past 60 years, with many satellite systems still relying on it to this day.
Green thrusters – propulsion systems that avoid the use of compounds like hydrazine – provide a much safer means to power satellites and other spacecraft. And over the past decade, the technology has really started to gather pace, in part due to concurrent breakthroughs seen with precious metal additive manufacturing (AM).
Freedom to Create
Traditional subtractive manufacturing is inherently restrictive due to its reliance on machining, casting and welding.
While useful in many cases, these techniques are ill-suited to the development of parts destined for use in the latest propulsion systems. They limit achievable geometries and make it harder to optimise designs – issues that are especially challenging for an industry that’s not only in a constant state of R&D but also in receipt of a significant amount of public money.
AM easily moves past these barriers, offering a much greater degree of freedom and flexibility in design. This is because the starting material – powdered alloys of precious and non-precious metals – are fundamentally different, only using precise amounts during production, allowing a team to work on prototypes that would otherwise be impossible to achieve.
Platinum, palladium and iridium are all commonly used in thrusters due to their stability, resistance to high-temperature oxidation and excellent catalytic properties. Platinum and iridium are especially valuable because they facilitate the decomposition of green propellants, such as NASA’s AF-M315E and other ionic liquid-based alternatives to conventional fuels. The high catalytic activity of these metals supports a quick, reliable reaction at lower temperatures, which is especially important for fuels like AF-M315E and LMP-103S as they are typically harder to ignite when compared with hydrazine.
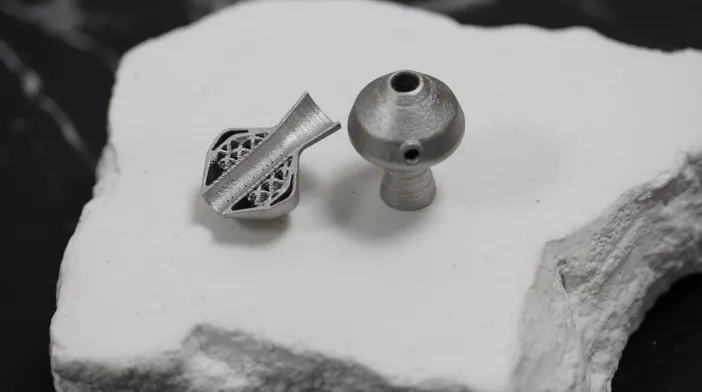
Internal lattice structures and microchannel networks are perhaps the best examples of how AM is pushing aerospace development forward. These designs optimise a thruster’s ability to handle heat while also better controlling the flow of propellant gases. Such complex structures are essential for green thrusters, as they improve fuel efficiency and reduce emissions by precisely controlling combustion processes within a satellite.
With subtractive manufacturing, the production of lattices would create high volumes of unused material, not to mention take hours to machine to a satisfactory standard without sacrificing the integrity of a component. Given that the cost of working with precious metals is already high, these traditional techniques are not just impractical but can effectively price-out important parts of the development process. That is, unless engineers engage with experts in this field, like those at Cookson Industrial, who are able to minimise material losses.
Built to Last
Precious metal AM is also improving the durability and expected working life of green thrusters. This is another huge advantage for an industry spending vast amounts of time and money on development, not least when some components will only be minor features in a much larger design.
While more environmentally friendly than hydrazine, green propellants still operate at very high temperatures, and some are also highly corrosive. Precious metals, particularly those in the platinum group, exhibit strong corrosion resistance, making them ideal for designs destined to work in harsh environments over long periods. However, to get the most out of these properties, the chosen metals have to be engineered a certain way.
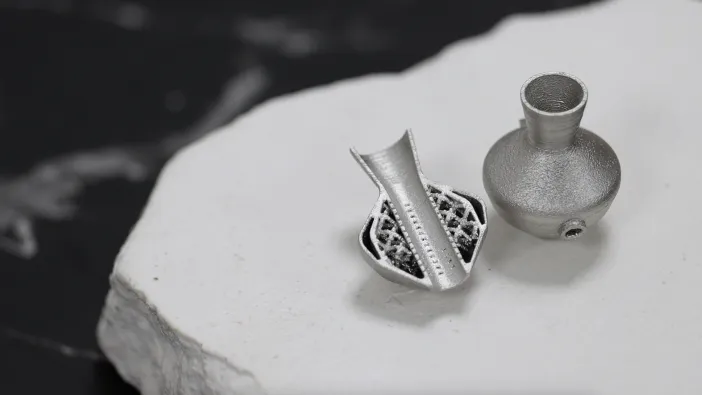
Tighter control of a metal’s microstructure during printing is where AM really comes into its own. Fine tuning a microstructure at a microscopic level – with techniques like laser powder bed fusion – can significantly improve a thruster’s resistance to thermal cycling and fatigue. This durability is particularly relevant for green thrusters that may undergo frequent start-stop operations, such as in satellite attitude control systems or orbital manoeuvring engines.
While not the principal goal for green thrusters, a higher degree of durability is important for lowering the impact of each mission. It leads to longer lifespans and a reduced maintenance programme, as replacement parts are needed much less frequently. Eliminating use of hydrazine is front and centre for this area of research, but added benefits of this kind are still important for the overall sustainability of work in space.
Where Worlds Collide
AM may be unlocking the full potential of precious metal applications in space but there are several confronting issues for those without the right knowledge or experience.
It will come as no surprise to learn that powdered precious metals are incredibly expensive. Five kilos of platinum – roughly the amount needed to print 6-8g parts – costs around £140,000, though in recent times the price has gone well beyond that due to supply chain pressures. Other potentially useful precious metals, like Rhodium, cost far more simply because they that much rarer.
Good handling practices are therefore critical when working with powdered precious metals. The risk of loss is still high even with good equipment because the amount of material that could send a project’s total cost spiralling is effectively microscopic.
This situation has led to closer collaboration between companies with an established history of working with precious metals and those in aerospace seeking to develop parts quickly and cost-effectively. In Cookson Industrial’s case, the company has been able to print platinum inserts for in-space water thrusters while achieving losses of less than 1%. This is only possible through the use of specially modified machines designed to capture and redirect as much loose material as possible, in addition to strict workflows for personnel that limit contact with all powdered materials.
Green thrusters may still be some way off replacing hydrazine-based designs, though it’s clear this area of research has benefitted significantly with the advent of AM, not least when overseen by those with an expertise in metallurgy.
For more information on precious metal AM, visit: www.cookson-industrial.com
Cookson Industrial to Showcase the Potential for Precious Metal Additive Manufacturing at Southern Manufacturing
Cookson Industrial aims to showcase how UK subcontractors can unlock the potential of precious metals in advanced manufacturing applications at Southern Manufacturing & Electronics Show 2025 (4-6 February 2025).
The stand (A315) will include a range of example components produced using precious metal additive manufacturing (AM), as well as samples of the company’s gas atomised precious metal powders, industrial precious metal refining, and semi-finished capabilities. The use of precious metals in these areas offers subcontractors a new frontier for material performance in extreme environments, where traditional alloys have failed to meet the thermal and material application challenges presented.
Part of HM Precious Metals, Cookson Industrial aims to help organisations looking to explore the use of precious metals in industrial applications to de-risk their development, simplify their supply chains, and shorten time to market.
Aerospace is a key growth area for Cookson Industrial, where the company is helping deliver new satellite thruster designs to help decrease the weight of components and reduce the volume of hazardous materials such as hydrazine which are traditionally used in the manufacture of chemical thrusters.
Cookson Industrial’s state-of-the-art additive manufacturing facility is located in Birmingham. This currently comprises EOS Precious M 080 and M 100 AM machines, alongside a Renishaw AM 500S Flex single laser AM machine.
The company’s cutting-edge precious metal AM solutions offer a gateway to quality and innovation in the realm of 3D printing, a service which has seen increasing demand within the industry. Visitors to Southern Manufacturing & Electronics Show are invited to see what Cookson Industrial can offer by speaking to its expert team and exploring AM printed pieces such as lattice structures – highlighting the complex designs the company can produce.
Nikesh Patel, Head of Cookson Industrial, comments: “The Southern Manufacturing & Electronics Show is a fantastic opportunity for us to showcase our new products to the UK’s subcontract manufacturing base, especially given their role in the country’s burgeoning aerospace industry.
“Previously, the use of precious metals in manufacturing has largely been confined to jewellery and luxury lifestyle applications. We are pushing to redefine precious metals for AM and visiting us at the show will clearly demonstrate the leaps and bounds we have made towards exploring its potential for use in performance-critical manufacturing applications.”
For more information on precious metal AM at Cookson Industrial, visit: www.cookson-industrial.com.